Several common types of plastic are used to manufacture plastic bottles for the pharmaceutical industry:
- HDPE (high density polyethylene)
- LDPE (low density polyethylene)
- PP (polypropylene)
- PET (polyethylene terephthalate)
Each plastic resin type has unique characteristics and properties that work for different product forms, such as tablets, liquids, creams, softgels, sprays, etc. It’s important to choose the correct material and know how to identify the defect types that can occur during the manufacturing process. Plastic bottle defects can compromise your product and your profitability. At Drug Plastics, we want to help you recognize defects, avoid downstream problems, and keep your business running smoothly.
Identify the Most Common Defects in Plastic Packaging
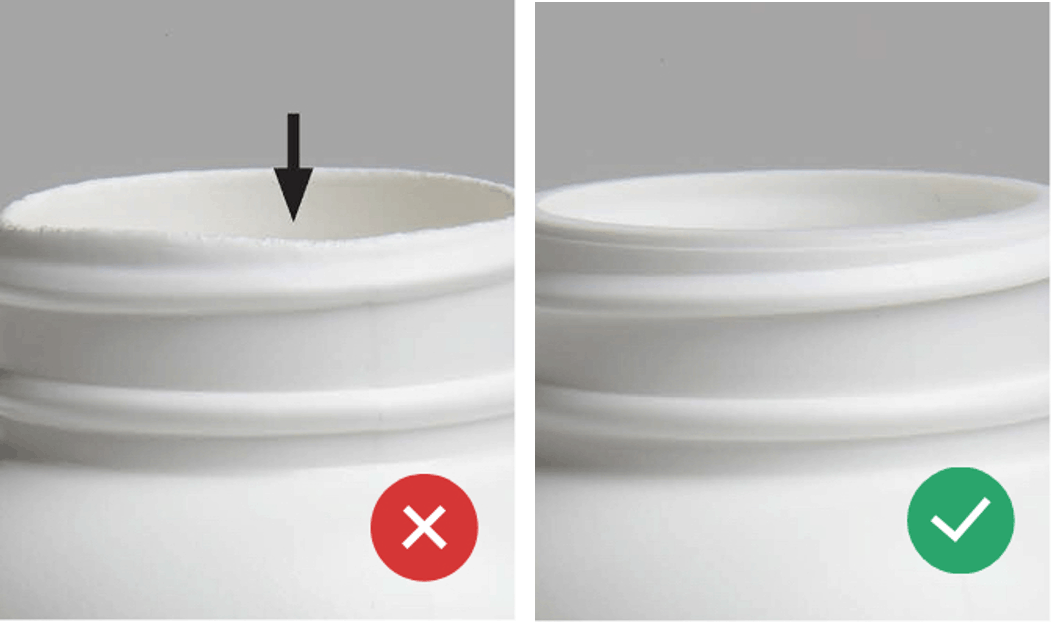
Uneven Sealing Surface: The top area where the bottle is sealed is one of the most important parts of a packaging system. If the bottle top is uneven, it can result in an improper seal, and increase the chance of product contamination.
In addition, an uneven seal also undermines the perception of your brand to consumers; no one would purchase a product if the seal is compromised or the bottle top is defective.
At Drug Plastics, you will have peace of mind that your product will be secure and protected because our bottles and closures work together properly. We manufacture our own bottles and closures so you can rest easy knowing that they will work together as a system no matter what product goes inside.
Individual states are putting more emphasis on child resistant packaging for many healthcare, wellness, and lifestyle products. Get ahead of these regulations with defect-free child resistant packaging from Drug Plastics – our products will increase the security of your product and reinforce customer trust in your brand.
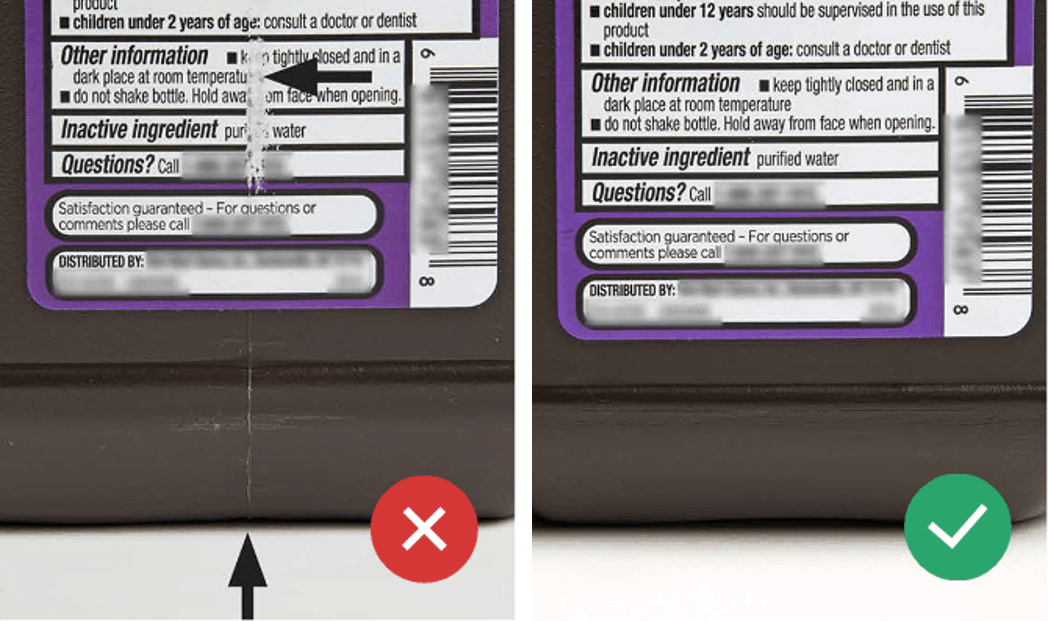
Raised Mold Seams: Knowing what ingredients a product contains is essential information consumers use to make buying decisions is important in today’s market. If labels are illegible, consumers can’t find necessary information they need to make educated choices, compare products, or understand proper dosages. This undermines brand loyalty and causes many consumers to choose a different product.
More and more information is required to be present on a label, and the print is getting smaller. This trend makes it all the more important for your labels to lay flat on prescription and over-the-counter medication bottles. Raised mold seams (or parting lines), can cause illegible labels.
All of our plastic bottles have smooth seams, ensuring that labels are easy to read and look great. State-of-the-art machinery, software and production processes ensure that our bottles are consistently manufactured – every time. Labels will lay flat, be even, unwrinkled and readable, making your product stand out and look professional.
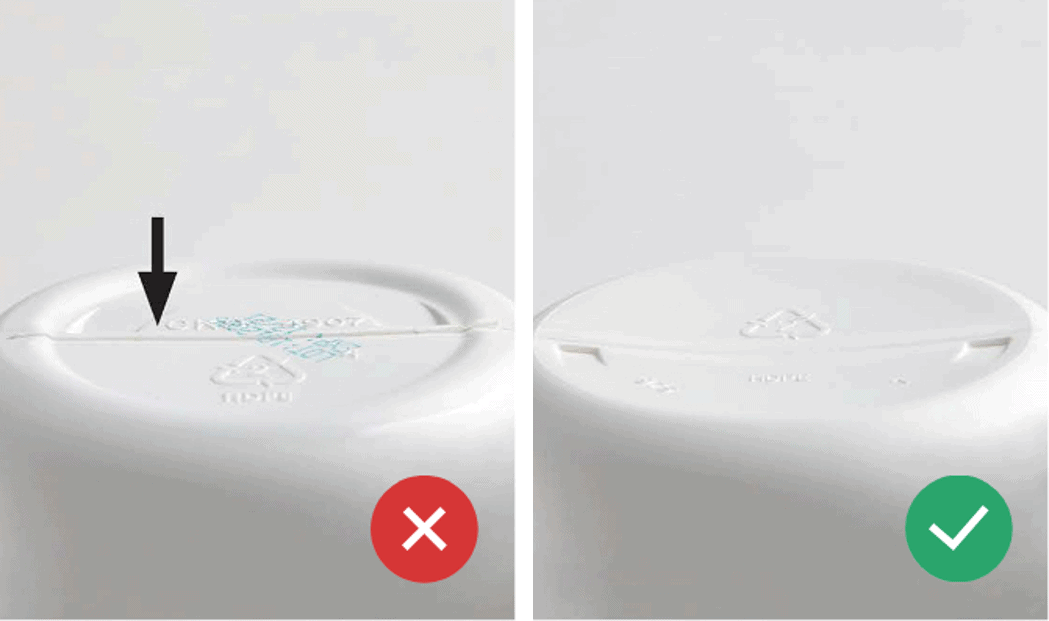
Excess Bottom Flash: Bottles that don’t stand up properly can cause big problems for your brand. Imagine bottles displayed on retail shelves that are tilting, uneven or falling over. Even worse is when the bottles are not stable for consumers to store at home.
This issue can be caused by excess bottom flash that is not removed during the manufacturing process. Bottles will be unstable and not stand straight if this excess material isn’t removed properly. In addition, excess flash can also result in a poor printing surface and a mediocre brand impression.
At Drug Plastics, our bottles are manufactured to ensure stable bottoms, a quality print surface, and will leave a superior brand impression with your customers.
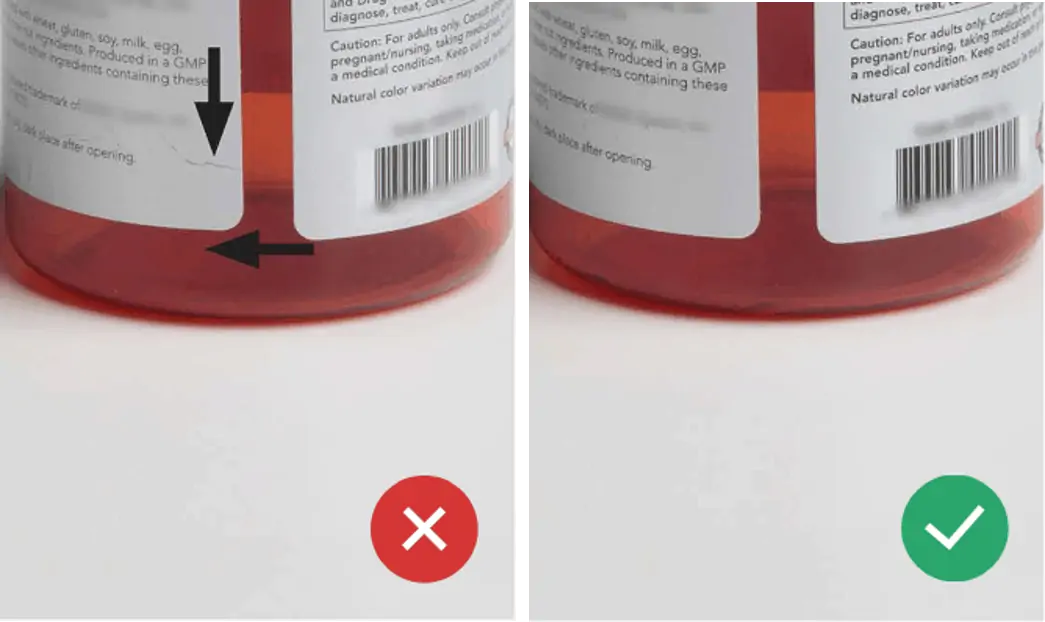
Uneven Sides: Bottles that are manufactured with uneven sides result in crooked and wrinkled labels that decrease copy readability and look unprofessional. As we discussed, labels are a vehicle to complement your brand, showcase information about your product, and help instill consumer confidence. A label must also include all of the required regulatory information for your industry.
Our bottles are manufactured with even sides, ensuring that labels lie flat, evenly wrap around the bottle, and look professional. Defect-producing issues have been engineered out of our manufacturing processes, producing bottles and closures that are virtually perfect each time.
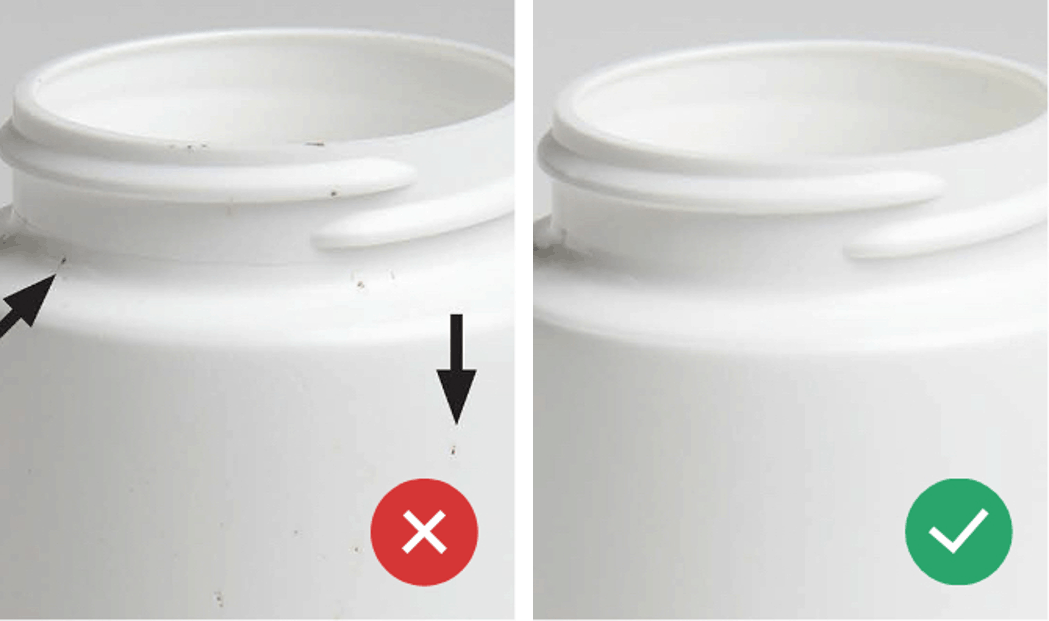
Foreign Material: Consumers loose trust and confidence in a brand when plastic bottles look cloudy or dirty. It also impacts the product’s perceived safety — no one wants to purchase a product that has a dirty container. A dirty or cloudy appearance can be caused from carbonized resin or trapped material inside the resin during the manufacturing process.
Our bottles are rigorously inspected to ensure that foreign material stays out of our raw materials and out of our manufacturing processes. Our bottles look crisp and clean. Every time.
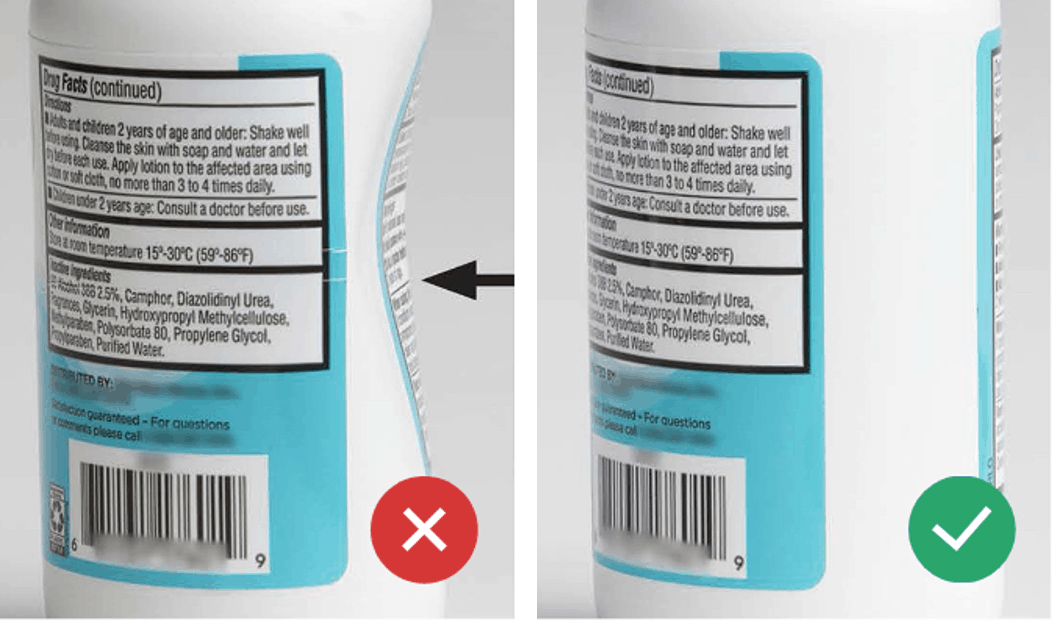
Improperly Spec’d Material: This defect is caused by selecting the wrong type of material for the intended package. In simple terms, the type of plastic packaging being used is not meant for the type of product it contains, or it is not the correct weight. The bottle could also be the wrong size or strength.
Deformities or degradation of the bottle happens when bottle material isn’t properly spec’d, or if the wrong size bottle is spec’d. To consumers, the packaging you use represents your brand — if it looks deformed, it can result in reduced consumer confidence and lost sales.
At Drug Plastics, we carefully spec the correct material for each and every job, ensuring that the bottle integrity is maintained, the packaging is aesthetically pleasing, and they won’t appear damaged or unstable to consumers.
The Bottom Line
It’s important to recognize defects when selecting plastic packaging for your pharmaceutical products. Perfection isn’t easy. We have engineered our manufacturing processes to focus on the highest quality requirements for every bottle and closure we make. When you work with us, we can help you learn to recognize defects and select the perfect product packaging made to fit all of your specifications. We can help increase your profitability, reduce the risk of product recalls, and reinforce your brand.
Reach out to one of our experts by calling 610-367-5000.