Custom Design Plastic Bottles and Closures Made Exclusively for You
Sometimes a stock PET bottle, standard HDPE bottle, or an off-the-shelf plastic closure is not sufficient. What you really need is custom packaging. At Drug Plastics, we understand that you may want your product to look special. Perhaps there are filling equipment, regulatory, labeling, light sensitivity, or other packaging requirements you must address as well. We’ll make it easy for you to get the perfect custom plastic bottle and closure for your product.
Understanding Your Requirements
We begin every custom project with a single goal: to thoroughly understand how you want the plastic packaging to look and the specifications it must meet. We call this process requirement gathering. Capturing these qualitative and quantitative details facilitates an on-time, on-budget, and on-target custom design plastic packaging solution.
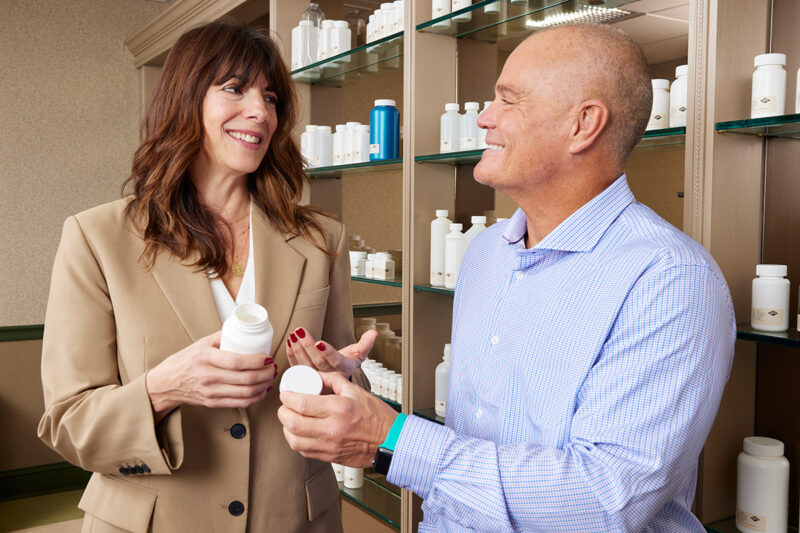
Evaluating Initial Concepts
Depending on your requirements, there may be several ways to achieve the desired look and specifications of your custom design plastic bottle or closure. We’ll provide you with all of the design options that meet your needs so that you can decide the best direction for your packaging.

Identifying the Best Resin Type for Your Bottle
There are many different types of plastic resin used to make bottles and closures: High Density Polyethylene (HDPE); Low Density Polyethylene (LDPE), Polyethylene Terephthalate (PET); and Polypropylene (PP). Each different type of resin has unique properties which may or may not be advantageous for the product that will be packaged inside. We can help you determine which resin is the right choice for your product.
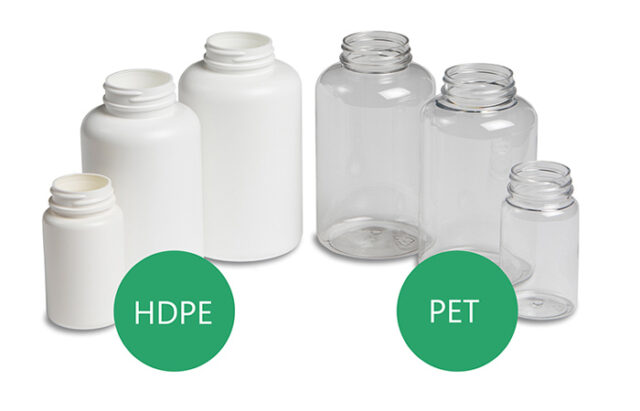
Selecting a Color for Your Product Packaging
Is color part of your brand identity? If so, color selection is a critical part of the packaging design process. All of our pharmaceutical bottles, vitamin and supplement packaging, lifestyle packaging, and plastic closures are available in a wide variety of color options to fit your needs. Our knowledgeable experts will work with you to identify what’s important for your brand and select the option that is most cost-effective for your packaging.
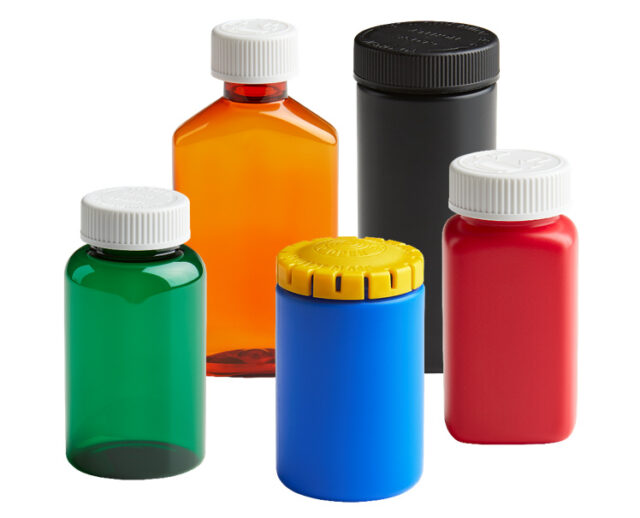
Determining the Correct Closure Liner for Your Product Packaging
Did you know that certain closure liners are designed for liquids and others are designed for solid dose medications? Closure liners are specifically designed for different types of products: choosing the proper closure liner will not only protect your product and the consumer, it can also save you money. It’s important to understand the materials used to manufacture closure liners and the questions to ask to determine which type of liner is best for your plastic bottle.
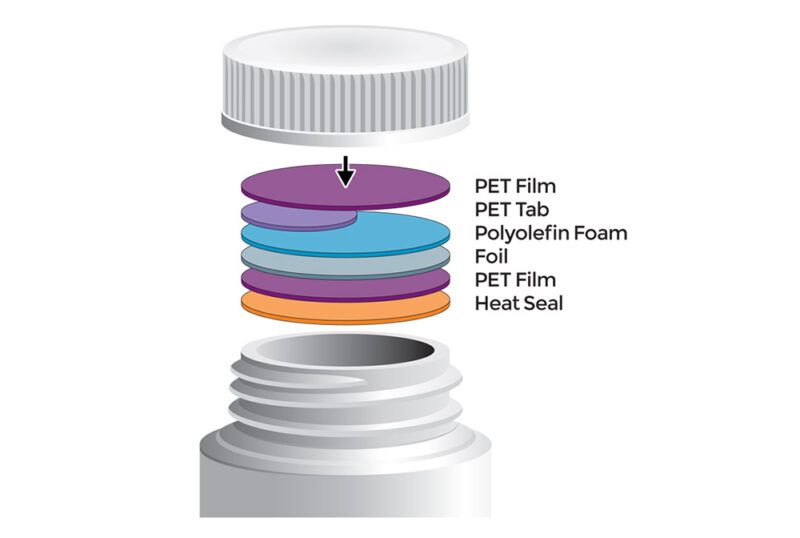
Choosing the Best Manufacturing Process
Drug Plastics uses four distinct types of blow molding: Extrusion Blow Molding (EBM), Compression Blow Molding (CBM), Injection Blow Molding (IBM), and Injection Stretch Blow Molding (ISBM). The size and bottle geometry, along with the type of plastic resin being used, determine which manufacturing process is best. With over 60 years of bottle making experience, our experts will help you to select the best molding process for your plastic bottle.
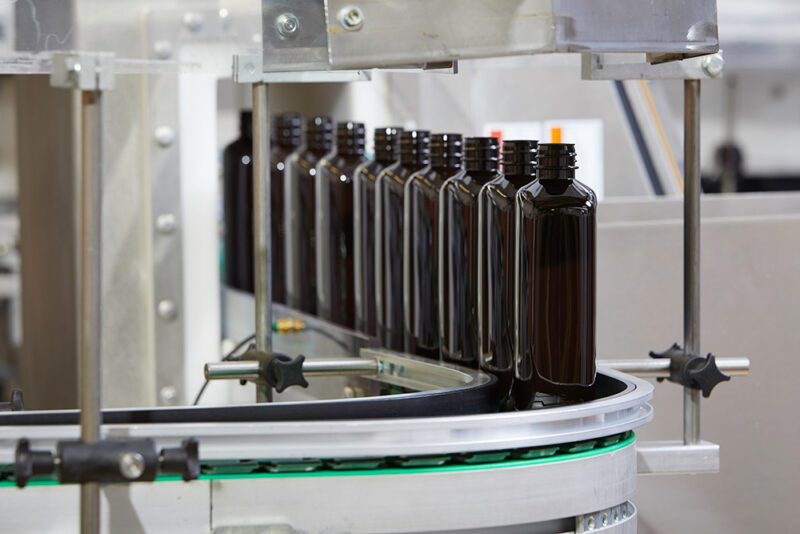
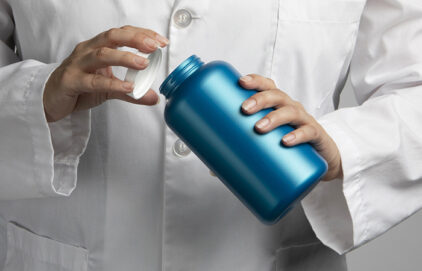
Engineering for Flawless Integration
Plastic bottles and closures must be engineered to work seamlessly. The closure must seal perfectly. The bottle must be designed to meet labeling or filling requirements. Both items must function efficiently within the dimensional requirements of the filling operation. You can rest easy knowing our experienced team of engineers will ensure your product meets these requirements.
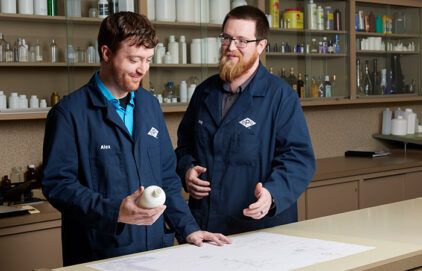
Designing the Perfect Form
Our in-house designers will create a detailed CAD product drawing outlining every critical dimension of your HDPE bottle, PET bottle, or plastic closure. This drawing will provide the direction needed to create manufacturing molds. It will also be a reference check to ensure that the product we make meets your specifications.
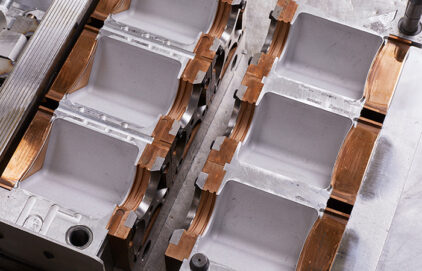
Crafting the Elemental Mold
Drug Plastics has its own mold-making facility. Our engineers design, fabricate, qualify, maintain, and repair our molds. Our capabilities range from unit-cavity prototype molds through multi-cavity production molds. We build the highest precision tools using high-grade materials and proprietary technologies we have developed in-house. This ensures that our molds produce a consistent product, perform exceedingly well under high production demands, and provide a higher ROI for your plastic packaging.
Maintaining the Highest Quality Standards
While most companies claim to make a quality product, few claim to make a perfect product. For years, we have said we are “A Family of Perfect Quality.” Rightfully so.
Materials, equipment, and decades of process knowledge come together to create uniformity and unequaled consistency. That’s why each plastic bottle and closure we produce is virtually perfect and identical, every time.
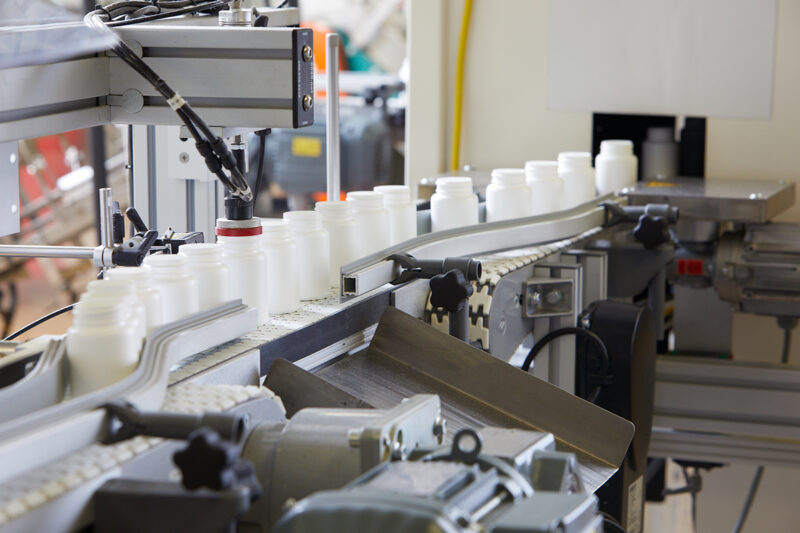
Ensuring Quality Throughout the Process
Drug Plastics has earned the designation of ISO 15378 Certified. Not only are our manufacturing processes controlled and monitored to make plastic bottles and closures right the first time, but we also have backup systems that inspect each product. Error detection devices, random sampling and testing, and a Quality Control department ensure 100% conformity. We strive to ensure that you never receive anything unexpected.
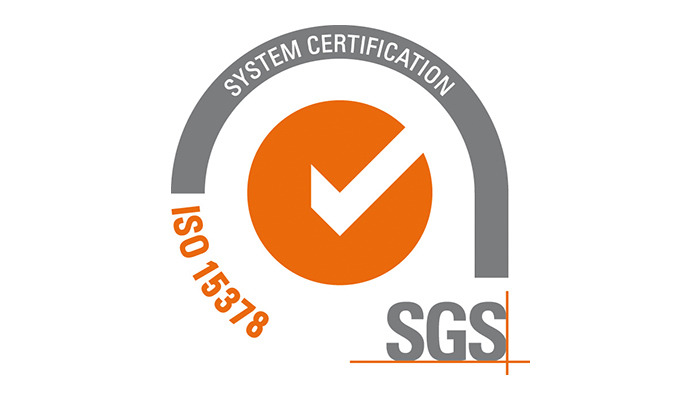
Delivering Support and Service
Our commitment to you does not end when the product arrives. You can depend on Drug Plastics to get answers and assistance. We are here to make sure you are satisfied and happy with your purchase. As a manufacturer ourselves, we know that many companies claim to have great service, but fail to provide it. We promise to continue earning your business and trust by being responsive and dependable.