The Advanced Recycling Process
Advanced Recycling is the emerging sustainable method to obtain ethylene molecules needed to produce polyethylene. Post-consumer waste and several other feedstocks (specific chemical ingredients) are used to generate identical ethylene molecules.
In addition, the Advanced Recycling process ensures that the resulting virgin resin is identical to virgin resin produced from fossil fuels, like oil and natural gas. Like all virgin resins, resin produced through the Advanced Recycling process is free from foreign material and other contaminants.
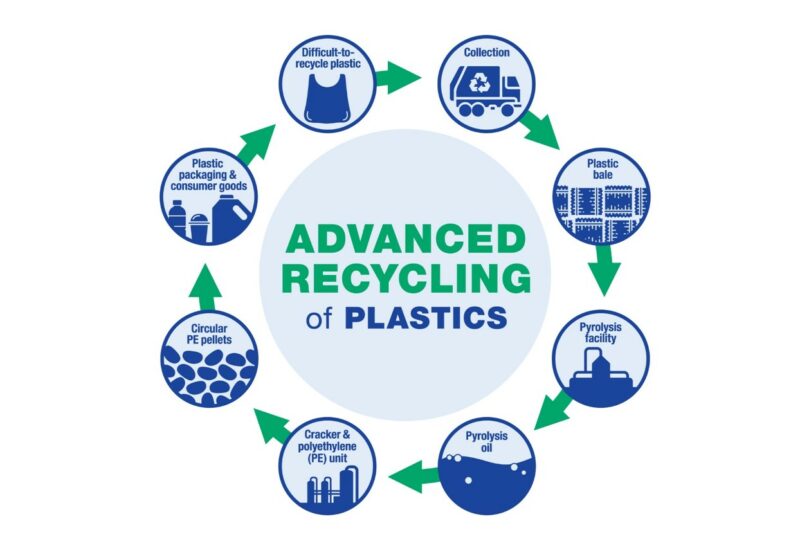
Today, resin manufacturers use fossil fuels to create the primary feedstocks for plastic resin production.
These feedstocks are converted into plastic resin through chemical reactions.
For polyethylene production, the feedstock is a double hydrocarbon molecule called ethylene.
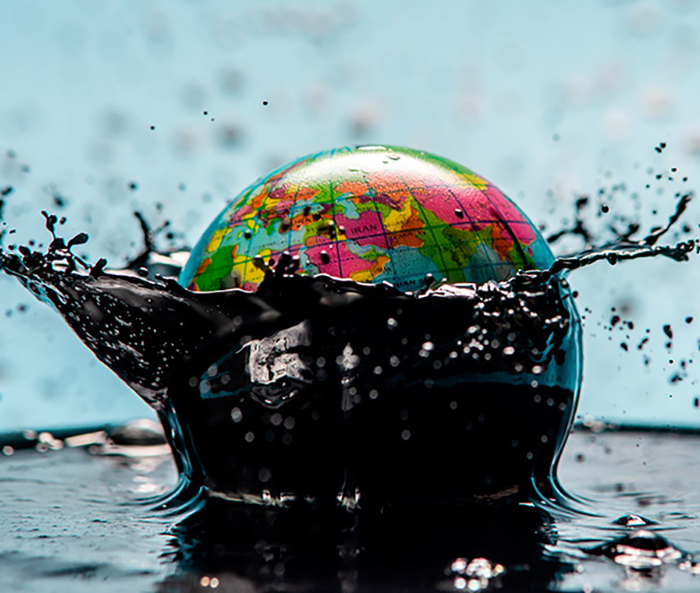
Plastic resins are made of polymers: molecules containing many repeating hydrocarbon units.
The plastic resin manufacturing process first subjects natural gas and petroleum feedstocks to “cracking“ – a heat-intensive process which purifies ethane and changes it to ethylene.
The ethylene is then subjected to chemical reactions that grow the number of carbon atoms until the correct length polyethylene polymer is formed.
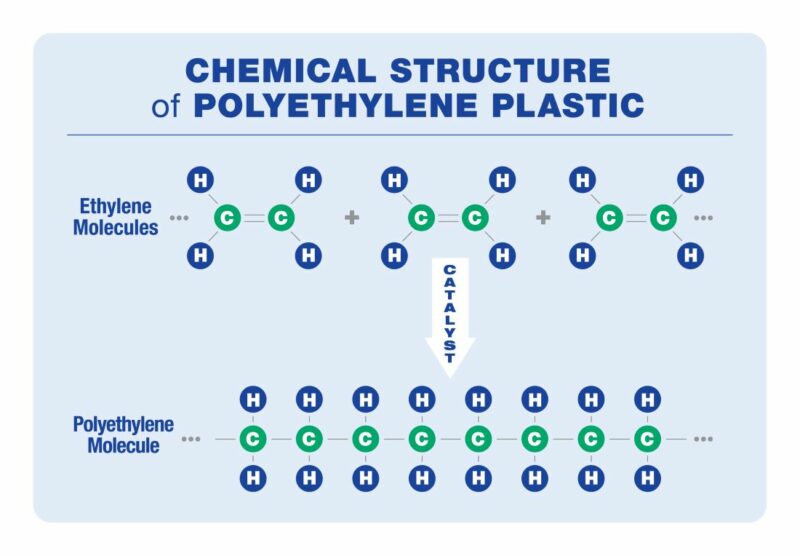
In the Advanced Recycling process, post-consumer plastic waste and biomass are heated in a non-combustible, oxygen-free pyrolysis process.
The pyrolysis process is the key to obtaining ethylene molecules from post-consumer waste. This creates pyrolysis oil.
Pyrolysis oil is then processed through the same reactors as natural gas and crude oil, creating the same ethylene molecules. The ethylene molecules from all sources are then used to create the virgin resin.
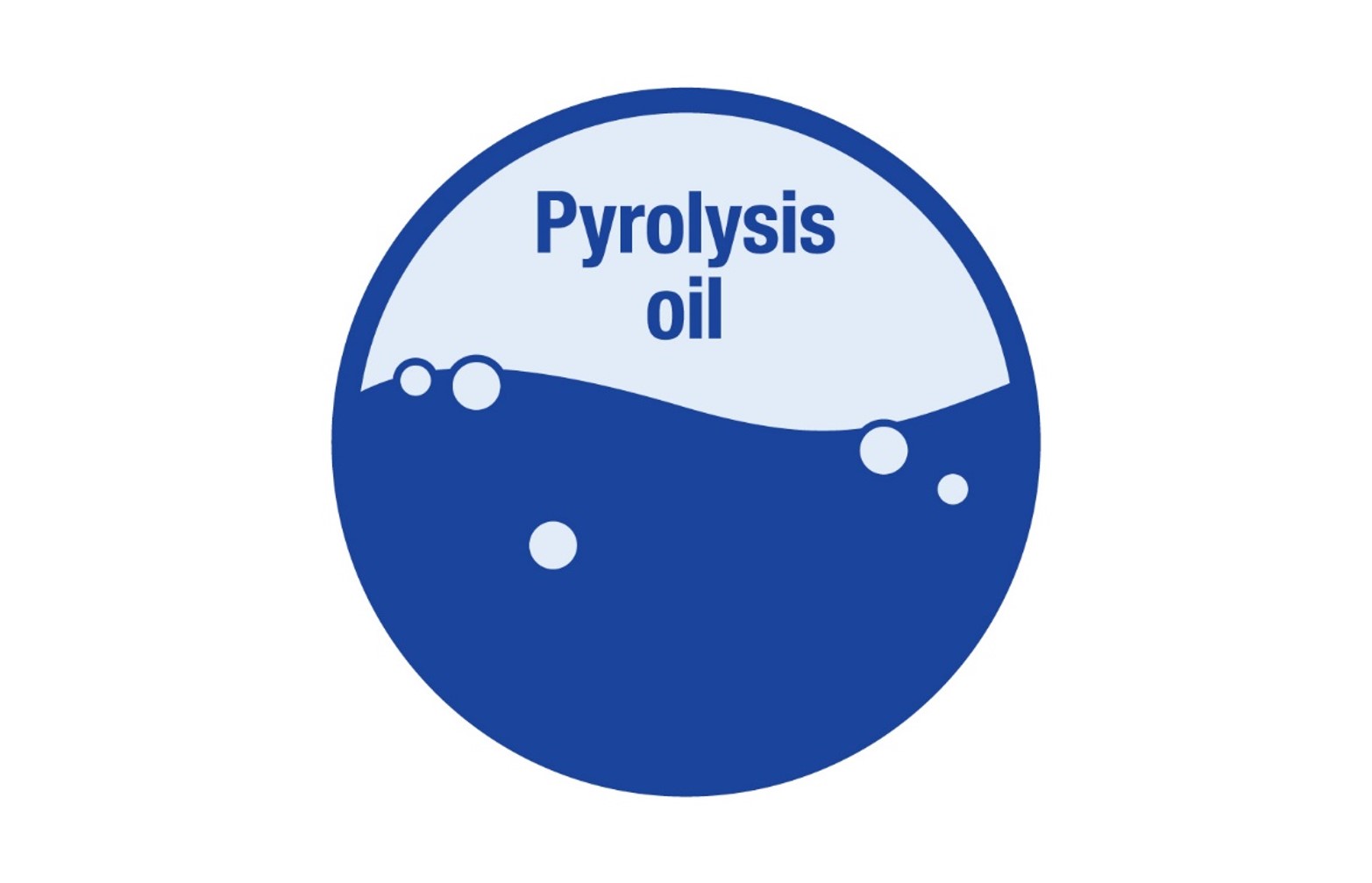
This graphic shows the Advanced Recycling process as well as the other three polyethylene resin production processes:
- Virgin resin production from fossil fuels
- Post-Consumer Recycled (PCR) resin produced through the Mechanical Recycling process
- Virgin resin production using bio-based feedstocks
Advanced Recycling mixes ethylene molecules obtained from multiple feedstocks, producing virgin plastic resin. This process creates a Circular Economy. Resin made through Advanced Recycling is a continuous loop: plastic waste is processed repeatedly, without any reduction in physical properties. This is the definition of sustainable.
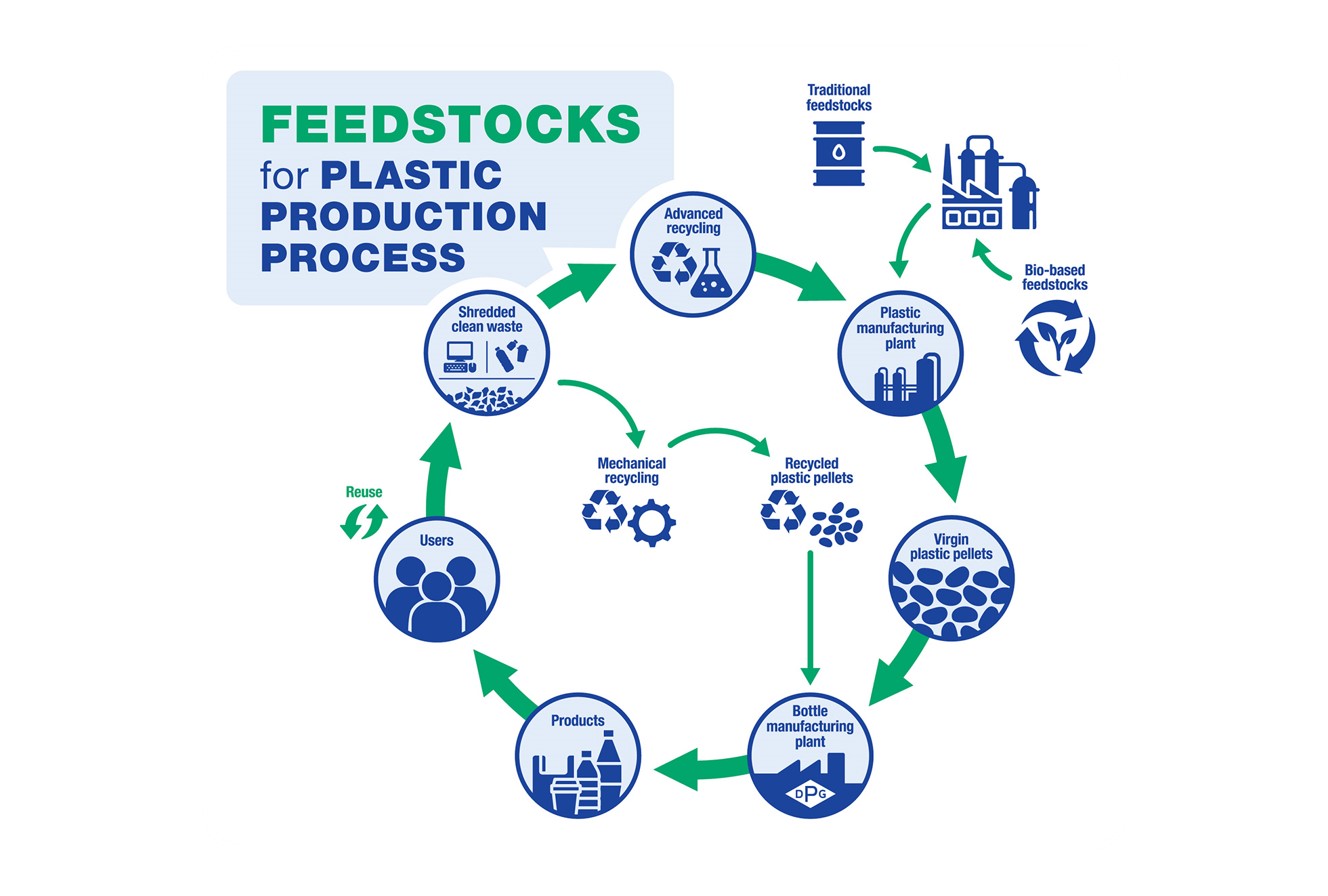
The ethylene molecules needed to create polyethylene can be obtained through multiple sources, like fossil fuels, plastic waste, and biomass. Each batch of polyethylene can vary in the amount of ethylene molecules derived from these sources. The goal is that the majority of molecules in the resultant plastic resins are sustainably created through this Circular Economy.
Similar to the energy grid that utilizes sustainable power sources like solar, wind, and hydro, the Mass Balancing method allows Drug Plastics and our customers to purchase certificates. These certificates designate a specific amount of resin pounds that are supported by Advanced Recycling. In addition, customers can claim the use of recycled material for designated products up to the amount of certificate pounds purchased.
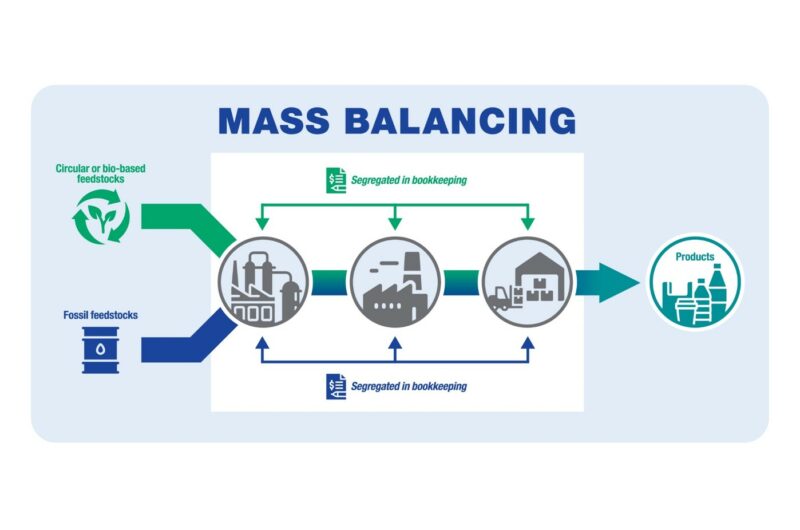
How to Choose
Resin selection is an important step in the product packaging design process. There are notable differences between resins and much to consider during the selection process.
Advanced Recycling has numerous advantages for increased sustainability. If you’re looking for virgin resin that keeps plastic out of landfills and helps to create a Circular Economy, then switching to resin produced from feedstocks generated in the Advanced Recycling process may be the right choice.
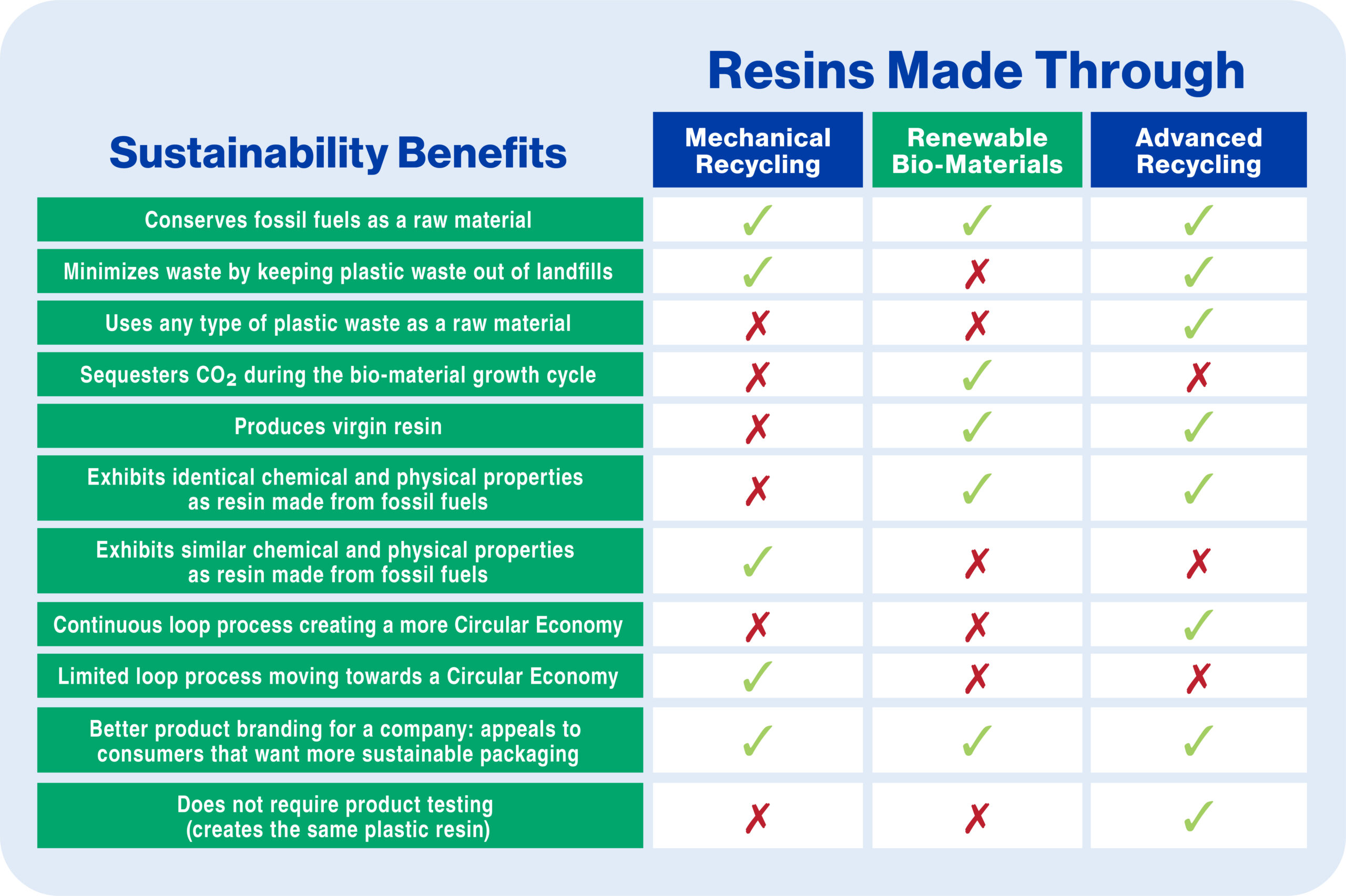
Read our in-depth article and learn more about Advanced Recycling and Mass Balancing. Understand how to positively affect the environment, lessen reliance on fossil fuels, and reduce the amount of plastic waste that goes into landfills.
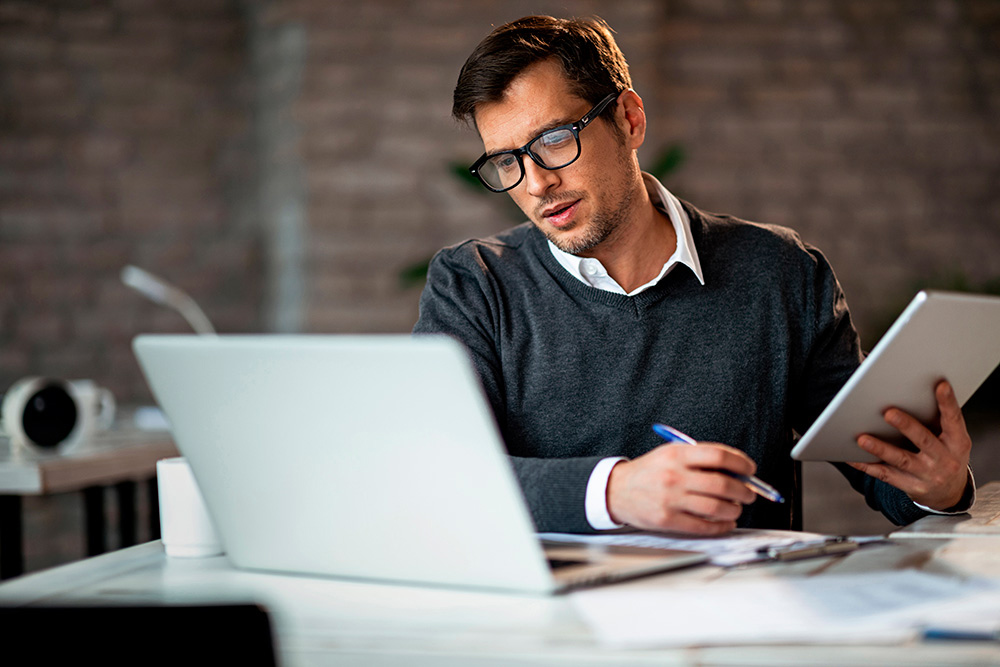